This guide explores the nuances of rubber diaphragm seals, including their design, materials, maintenance practices, and why selecting the right seal matters for optimized performance. With insights into industry practices and trends, this resource ensures you have all the information needed to choose and maintain the ideal rubber diaphragm seal for your needs.
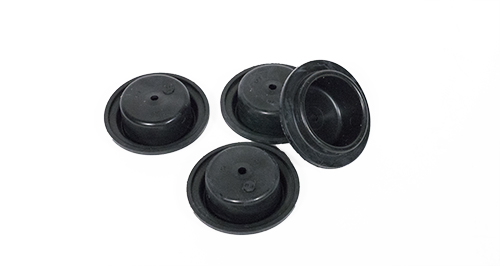
What Are Rubber Diaphragm Seals?
Rubber diaphragm seals are thin, flexible membranes engineered to create a barrier between different media, such as liquids and gases, while allowing controlled motion or pressure transmission.
Key Characteristics
- Dynamic Performance: Designed to handle repetitive motion without compromising the seal.
- Flexibility: Can adapt to a wide range of pressure and temperature conditions.
- Chemical Resistance: Many diaphragms are made to resist aggressive chemicals, oils, or gases.
Applications Across Industries
- Automotive Systems: Fuel pumps, braking systems, and air suspension systems depend on diaphragms for efficient operation.
- Industrial Equipment: Compressors, actuators, and valves utilize rubber diaphragms for sealing and isolation.
- Medical Devices: Precise operation in equipment like ventilators and infusion pumps relies on these seals.
- Aerospace: Used in hydraulic and pneumatic systems to ensure optimal performance under extreme conditions.
How Rubber Diaphragm Seals Work
Rubber diaphragm seals work by creating a flexible yet robust barrier that prevents leakage and contamination. Their operational design is dictated by their intended use.
Functionality
- Pressure Regulation: By flexing to accommodate pressure changes, the diaphragm maintains system balance.
- Media Isolation: Prevents mixing of different substances, crucial for sensitive applications like chemical processing.
- Dynamic Sealing: Accommodates motion while maintaining a tight seal, ideal for valves and pumps.
Operational Factors
- Stroke Length: Determines the diaphragm's flexibility and durability.
- Media Compatibility: The diaphragm material must resist degradation from the fluid or gas it interacts with.
- Temperature Range: Ensures consistent performance across varying environmental conditions.
Design Considerations for Rubber Diaphragm Seals
Designing an effective rubber diaphragm seal involves multiple considerations, from geometry to reinforcement. Each factor plays a significant role in ensuring the seal meets performance expectations.
1. Geometry and Shape
- Flat Diaphragms: Cost-effective solutions for basic applications with minimal motion.
- Convoluted Diaphragms: Feature a wave-like shape for increased flexibility and range of motion.
- Rolling Diaphragms: Offer superior durability by reducing friction during operation.
2. Material Selection
Choosing the appropriate rubber diaphragm material is critical for long-term functionality. For instance:
- Nitrile Rubber (NBR): Known for oil and fuel resistance, making it a popular choice for automotive and industrial use.
- Silicone Rubber: Preferred for high-temperature applications in medical and food industries.
- Fluorocarbon (FKM): Exceptional chemical resistance, ideal for aerospace and chemical processing.
3. Customization Needs
Modern manufacturing allows for significant customization in diaphragm design, including thickness, reinforcement, and specific material formulations. Partnering with experienced rubber diaphragm manufacturers ensures the best results for specialized applications.
Materials Used in Rubber Diaphragm Seals
Each material offers unique benefits tailored to specific operational needs.
1. Silicone Rubber
Silicone diaphragms are highly flexible and resistant to extreme temperatures, making them ideal for medical and high-temperature industrial applications.
2. EPDM Rubber
With excellent resistance to UV light, ozone, and weathering, EPDM is commonly used in outdoor applications such as HVAC systems and water treatment equipment.
3. Neoprene Rubber
Neoprene provides a balance of chemical and weather resistance, often used in automotive systems and sealing applications exposed to moderate environmental challenges.
4. Fabric Reinforcement Options
In high-stress applications, fabric-reinforced diaphragms are indispensable. Commonly used reinforcements include:
- Nylon Fabrics: Offer durability and flexibility for high-pressure systems.
- Polyester Fabrics: Provide superior wear resistance, ideal for demanding industrial environments.
Challenges in Using Rubber Diaphragm Seals
While rubber diaphragm seals offer numerous benefits, they are not without challenges. Identifying these issues can help mitigate potential problems.
1. Wear and Tear
Constant motion can lead to material fatigue over time, causing cracks or leaks. Solutions include:
- Selecting high-quality, fabric-reinforced diaphragms.
- Ensuring proper lubrication and minimizing friction.
2. Chemical Degradation
Exposure to harsh chemicals can weaken the diaphragm. Choosing materials like FKM or silicone ensures chemical compatibility.
3. Temperature Fluctuations
Extreme temperatures can cause material hardening or softening. Proper material selection is vital to maintaining performance.
Maintenance of Rubber Diaphragm Seals
Proper maintenance practices prolong the life of rubber diaphragm seals and ensure consistent performance.
Inspection Guidelines
- Visual Checks: Look for cracks, deformation, or discoloration.
- Performance Monitoring: Identify early signs of inefficiency, such as leaks or pressure drops.
Cleaning and Care
- Use non-abrasive cleaning agents compatible with the diaphragm material.
- Avoid using high-pressure cleaning methods that can damage the seal.
Storage Recommendations
Store diaphragms in a cool, dry environment away from direct sunlight or ozone sources to prevent premature aging.
Selecting the Right Rubber Diaphragm Manufacturers
Partnering with reputable rubber diaphragm manufacturers ensures access to high-quality products tailored to specific needs.
Factors to Consider
- Customization Capabilities: Ensure the manufacturer can provide custom designs, such as fabric-reinforced diaphragms.
- Material Expertise: Look for expertise in advanced materials like silicone, NBR, and FKM.
- Certifications and Compliance: Verify compliance with industry standards to ensure quality and reliability.
Future Trends in Rubber Diaphragm Seals
As technology evolves, rubber diaphragm seals continue to adapt to meet new demands.
Emerging Innovations
- Eco-Friendly Materials: Development of sustainable and biodegradable materials.
- Enhanced Durability: Advances in fabric reinforcement for longer service life.
Industry Growth
The demand for rubber diaphragm seals is projected to rise, driven by their increasing use in renewable energy systems, medical devices, and advanced automotive technologies.
Conclusion
Rubber diaphragm seals are vital for countless applications, providing unmatched flexibility, durability, and reliability. By understanding their design, materials, and maintenance, industries can ensure optimal performance and minimize downtime. Partnering with trusted rubber diaphragm manufacturers guarantees high-quality products tailored to specific requirements, making these components indispensable for modern engineering challenges.