This article systematically discusses what type of material should be chosen for the diaphragm, briefly introduces the performance of common materials, and provides performance optimization tips in application scenarios.
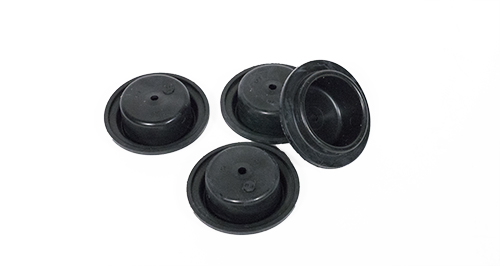
A Study on Role of Rubber Diaphragms
Some of the principle uses of rubber diaphragms include:- They work as barriers in such systems as well as in sealing applications that need precision and high durability. They reduce emissions, shield media, and facilitate the correct operation of pumps, valves as well as actuators. Unlike static seal rubber diaphragms are dynamic, they are flexed repeatedly during the operation and this flexibility requires high rubber resilience and reliability.
Mobile App Development Across Industries
Rubber diaphragms are integral to several industries:
Automotive: used in braking systems, fuel injection systems, and turbo chargers the rubber diaphragms retain pressure and avoid pressure leakage.
Industrial Equipment: Found in service as constant-use submerged diaphragm pumps, compressors, and control valves, these diaphragms control the flow of fluorescence in high-pressure conditions.
Medical Devices: Rubber diaphragms ease precision in the hardware components such as in ventilators, infusion pumps, and diagnostic products.
Aerospace: Dry at high altitude place diaphragms control fluidity and can handle the stress.
Selection criteria of materials play an influential role while designing and choosing the material for the product.
When selecting the type of rubber diaphragm, the individual requirements of a particular application must be considered out. Below are the most critical factors to consider:
1. Temperature Resistance
Fluency plays part, but it is obvious that operating temperature has a strong impact on material selection. Some examples of such materials include silicone diaphragms because they are capable of with standing high temperatures up to 200 °C. On the other hand, nitrile rubber (NBR) enthuses good characteristics at lower temperature.
2. Pressure and Stress Handling
Circulation of high-pressure fluids demand for stronger diaphragms that can effectively resist deformation. For such application, fabric reinforced diaphragms are normally preferred because fabric layer acts as additional reinforcement that can help not getting tired of the material.
3. Chemical Compatibility
If the system involves its exposure to aggressive chemicals, the choice of a chemically resistant material is inevitable. FKM is commonly used where the seals will exposed to oil, fuel and corrosive substances more often because of its superior performance in those conditions.
4. Environmental Conditions
Outdoor applications require materials that can offer protection from UV, ozone and withstand any natural conditions. Neoprene and EPDM rubber are preferred in the manufacturing of their products due to their endurance in extremes of high and low temperature.
5. Cost vs. Performance
Despite the fact, that they are more expensive at the beginning of the project, they also have the advantages of having low maintenance costs and long durability of the systems. Price sensitivity remains important, yet optimization of cost against quality is the most important factor.
Properties of Rubber Diaphragm Materials
Rubber material in fact has its own properties which are the characteristic of each of the material. Below are some common materials and their typical applications:
1. Silicone Rubber
It may be noted that silicone rubber has high heat resistance, flexibility as well as excellent chemical resistance.
Ideal Applications: Product Contact Materials, Medical device, Food processing equipment and High Temperature systems.
Advantages: Biodegradable, non toxic, approval from the Food and Drug Administration and good thermal stability.
2. Nitrile Rubber (NBR)
Due to this property, NBR find application where oil and fuel resistance are a requirement like the several automotive and industrial purposes.
Ideal Applications: Fuel systems, hydraulic pump, the oil & gas equipment etc.
Advantages: Inexpensive, tough, and nonflammable and does not swell from exposure to hydrocarbons.
3. EPDM Rubber
Thus, EPDM is suitable where it is exposed to steam, water or weather at working temperature.
Ideal Applications: Sanitary systems, ventilation, and conditioning systems as well as outdoor equipment.
Advantages: ultraviolet and ozone stability, and the affordability.
4. Fluorocarbon Rubber (FKM)
Due to chemical and high heat resistance FKM is used when mechanical stress is high.
Ideal Applications: Chemical industry , defense technology, aircraft, and industrial machinery.
Advantages: A low coefficient of thermal expansion, combined with excellent resistance to a variety of chemicals.
5. Neoprene Rubber
As an elastomer neoprene is semi-rigid, flexible, chemically and mechanically strong though weak to ozone and UV exposure.
Ideal Applications: Car, industrial and garden products sealing.
Advantages: Good UV resistance and reasonable resistance to chemical attack.
Choice of using Fabric-Reinforced Diaphragms
Where stress is high, the use of fabric reinforced diaphragms gives improved durability and performance. These diaphragms contain the fabric base of nylon or polyester with layers of rubber surrounding the material.
Key Benefits
Enhancement in desirability for use due to increase in the level of tear and puncture resistance.
Improved volumetric efficiency under high pressure.
The probability of having a material fatigue setback in case of considerable slicing and dicing movements is uncommon.
Use Cases
Automotive: In the case of brake systems and turbochargers.
Aerospace: Which occur in control systems in the environment that is characterized by high levels of altitude.
Industrial: In high pressure applications, pumps and valves.
Outline of Procedures for the Right Material Selection of Rubber Diaphragm
It means that the decision in choosing the material to be used must be carefully weighed and discussed. Follow these steps to make an informed decision:
Assess Operating Conditions
Describe the temperature, pressure and chemicals likely to be encountered by the diaphragm and the general environment in which it would be used.
Evaluate Material Properties
It’s much easier to compare silicone diaphragms with other similar products such as NBR or EPDM based on their advantages.
Consult Experts
Contact other rubber diaphragm makers so as to understand what specialized services are available and to determine material options.
Prototype and Test
Place the selected material through a set of operational realistic environment in order to determine its performance standards.
Some of the difficulties encountered in material selection for structural and infrastructural designs are discussed below.
Thus, while the range of options is impressive, the selection of proper material can become a problematic question. Common issues include:
1. Both over-emphasis on cost reduction and an over-concentration on performance can lead to serious failings in achieving objectives.
Other materials, such as FKM, are costly more than the other materials used in manufacturing seals, however they will prove worth the cost because the materials used will last longer and will be more resistant to chemicals than the other seals.
2. Ensuring Compliance
Medical and automobile industries often require that strict material standards must be met. That is why it is advisable to cooperate with manufacturers who have received certificates for using a diaphragm.
3. Lack of Quantitative Content Regarding Knowledge of Advanced Materials
Newer and better materials may not be well known hence the development of new steel. This is one of the issues that are best solved with the help of credible manufacturers.
Best Rubber Diaphragm Manufacturing Companies to Work with
Working with first-tier rubber diaphragm suppliers guarantees deliverability of quality products with optimal and current technologies. Seek for those manufacturers who conduct the production of exclusive patterns and have a wide range of materials for their products including fabric-reinforced diaphragms and modern rubber materials.
Conclusion
Choosing suitable rubber diaphragm material is perhaps the most important aspect in the reliability of the systems you are working on. The high variability of applications, assessment of material characteristics, and consultation with trusted vendors allow to make the best choice focused on performance and time.
Molded rubber diaphragms with heat resistant silicone diaphragms for medical applications or fabric reinforced diaphragms for various industrial uses, come down to meeting the intrinsic properties of the material type to the In particular, there is a marked need for heat resistant silicone diaphragms for medical applications and fabric reinforced diaphragms for usage in various industrial settings.